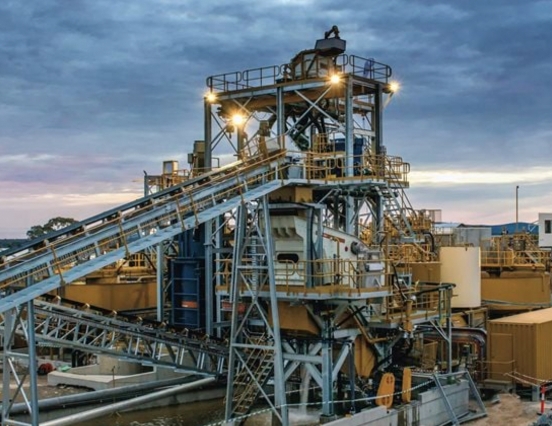
Decarbonization Strategies for Steel Manufacturing
Introduction
Globally, the iron and steel industry is responsible for approximately 8% of the total annual carbon dioxide emissions, while in India, it accounts for 12% percent of the total CO2 emissions. The industry heavily relies on coal as a reducing agent to extract iron from iron ore and to provide the carbon content.
The steel industry is at a pivotal moment as it grapples with the urgent need to address global climate concerns. Decarbonization has emerged as an imperative, pushing the industry to seek innovative strategies and transformative technologies for sustainable steel manufacturing. As a major contributor to greenhouse gas emissions, the industry’s transition to low-carbon and net-zero carbon solutions has become crucial. In this context, the industry must navigate a critical crossroads, embracing new approaches to tackle climate change and forging a path towards a more sustainable future.
This whitepaper addresses and provides answers to four key questions:
- What are the key challenges associated with carbon capturing ?
- How can CO2 gas be utilized in mining and enhance oil recovery ?
- What are the latest technologies for minimizing carbon emissions when utilizing coal in the manufacturing of steel?
- Which emerging technologies can enable net-zero carbon in the manufacturing of steel?
“Steel industry committed to decarbonization, emphasizing synchronized strategies and investments for clear technological pathways.”
Challenges in Carbon Capturing
(a) Cost:
High costs of CCS is a barrier to widespread adoption, especially in industries with narrow profit margins. Carbon Capture Utilization & Storage (CCUS) plant cost varies from $50 to $150 per metric ton to capture, transport, and to stored CO2.
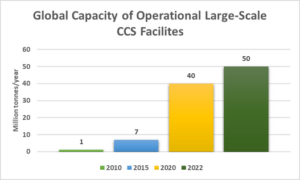
(b) Scale and Infrastructure:
To develop and to implement large-scale CCS infrastructure, including capture facilities, transportation networks, and storage sites, is an intricate and time-consuming process. On average, it takes 2 to 5 years to manufacture a CCS plant. However, larger or more complex projects may require 5 to 10 years or more for manufacturing.
(c) Regulatory and policy frameworks:
The development and implementation of CCS technology require supportive regulatory and policy frameworks. Governments need to provide clear and stable policies that incentivize investment in CCS projects, including financial support mechanisms such as grants, tax incentives, or carbon pricing mechanisms.
(d) Technology Innovation and Research:
By investing in technology innovation and research, governments, industries, and research institutions can drive advancements in CCS technology, making it more efficient, cost-effective, and viable for large-scale deployment.
Carbon Capture & Storage
“Carbon Capture & Storage (CCS) follows a three-step process: capturing carbon dioxide emissions from power generation or industrial activities like steel or cement production, transporting the captured CO2, and storing it deep underground.”
Carbon Capture & Utilization
Enhanced Coalbed Methane Recovery:
Coalbed methane (CBM) is a natural gas resource that can be extracted from coal seams. Injecting CO2 into unmineable coal seams can enhance the recovery of CBM. The injected CO2 adsorbs onto the coal matrix, displacing the methane and making it easier to extract. This process, known as enhanced coalbed methane recovery (ECBM), not only stores CO2 but also increases the extraction of a valuable energy resource. CO2 injection in coal seam gas reservoirs is termed as CarbonNet project in Australia.
Mineralization of Mine Waste:
CO2 can be utilized to promote the mineralization of mine waste materials. Mine waste, such as tailings or slag, can be treated with CO2 to promote the conversion of certain minerals into stable carbonates. This mineralization process not only sequesters CO2 but also stabilizes and immobilizes potentially hazardous elements within the waste, reducing environmental risks. The CarbFix project in Iceland involves injecting CO2 into underground basalt formations to mineralize mine waste and capture CO2 emissions.
Acid Mine Drainage Treatment:
Acid mine drainage (AMD) is a significant environmental issue in mining, characterized by the release of acidic and metal-rich water. The Penn Mine project in California, USA where CO2 is injected in acid mine drainage (AMD) treatment in the mining industry.
This project aimed to address the acid mine drainage issues caused by the historic copper and zinc mine. CO2 was injected into the underground mine workings, reacting with the acidic water to increase pH and reduce acidity.
Enhanced Oil Recovery (EOR):
When CO2 is injected into an oil reservoir, it acts as a miscible or near-miscible fluid with the oil present. This means that CO2 can mix and dissolve into the oil, reducing its viscosity and improving its flow characteristics. The injected CO2 also increases the pressure within the reservoir, which helps to drive the oil towards the production wells. The Weyburn- Midale field in Saskatchewan, Canada project is an example of CO2 injection in enhanced oil recovery (EOR) and demonstrates the dual benefits of this technique for both oil production and carbon storage. In this project, CO2 was obtained from a coal gasification plant in North Dakota, USA, and transported through pipelines.
CO2 Utilization in other Industries:
Rather than storing CO2 underground, captured CO2 can be utilized in various industrial applications, effectively converting it into valuable products and reducing emissions. Examples of CO2 utilization include using CO2 as a feedstock for the production of chemicals, fuels, polymers, or even carbon-neutral synthetic materials. Utilization offers an alternative to storage, turning CO2 into a valuable resource.
Low Carbon Emission Using Coal
Hydrogen injection technology:
Through the substitution of hydrogen for a portion of the coal in the steelmaking process, there is a substantial potential to reduce carbon emissions. Combusting hydrogen generates only water vapor as a byproduct, thereby eliminating or minimizing the emission of carbon dioxide (CO2), a significant greenhouse gas.
Studies and pilot projects have shown that the integration of hydrogen in steelmaking processes could potentially reduce carbon emissions by 20% to 80% compared to conventional coal-based methods.
By combining hydrogen injection technology with coal in steel manufacturing, the HYBRIT project in Sweden presents a pathway for achieving significant carbon emissions reductions in the steel sector while utilizing existing infrastructure and resources.
Biomass Co-firing:
When biomass is co-fired with coal, it serves as a renewable and lower-carbon alternative to coal. Biomass contains carbon, but since it is derived from recently living organic matter, the carbon emitted during combustion is considered part of the natural carbon cycle. This is in contrast to the carbon released from fossil fuel combustion, which adds to the overall carbon dioxide levels in the atmosphere.
The amount of carbon emission reduction achieved through biomass co-firing can vary. Studies and practical applications have reported potential emission reductions ranging from 5% to 20% or more, depending on the specific conditions.
The “GreenSteel” project initiated by Tata Steel in the United Kingdom serves as a project focusing on biomass co-firing in steel manufacturing.
Syngas Utilization:
Syngas is commonly generated through the gasification of coal or other carbonaceous materials, a process that converts the carbon content of coal into a blend of hydrogen (H2) and carbon monoxide (CO). Depending on the specific conditions and overall process efficiency, studies and practical implementations have shown potential emission reductions of 20% to 50% or even higher.
HIsarna is an innovative technology developed by Tata Steel in collaboration with several partners. The project aims to reduce the carbon footprint of steel production by integrating syngas-based ironmaking with a new type of blast furnace.
Net-Zero Carbon Technology:
Green Hydrogen-Based Steelmaking:
Green hydrogen is generated via the process of electrolysis, wherein renewable electricity is utilized to separate water into hydrogen and oxygen. This hydrogen can subsequently serve as an environmentally friendly and sustainable fuel option for steelmaking operations.
Green hydrogen-based steelmaking benefits are:
- When hydrogen is combusted or used as a reducing agent in steelmaking, it only produces water vapor as a by-product, eliminating CO2 emissions.
- Its production relies on renewable energy sources such as solar or wind power.
- It can be easily stored, transported, and utilized in various steelmaking applications.
Here are a few projects focused on green hydrogen-based steelmaking:
(1) HYBRIT (Sweden)
The HYBRIT project is a joint effort among SSAB, a Swedish steel company, LKAB, an iron ore producer, and Vattenfall, a utility company. The project’s objective is to substitute conventional coking coal with green hydrogen derived from renewable energy sources in the steelmaking process.
(2) H2Future (Austria)
The project aims to produce green hydrogen from renewable energy sources and use it as a reducing agent in the direct reduction of iron ore, eliminating the need for coal.
(3) Salzgitter’s SALCOS (Germany)
Salzgitter AG, a German steel company, is involved in the SALCOS project. The project focuses on developing a hydrogen-based steelmaking process that utilizes hydrogen generated from renewable energy sources.
Direct Reduced Iron (DRI):
DRI technology uses natural gas or hydrogen to reduce iron ore into metallic iron, bypassing the traditional blast furnace process. This eliminates the need for coking coal and significantly reduces carbon emissions. The project on DRI technology are HBI (Hot Briquetted Iron) plants and MIDREX® Process.
Electric Arc Furnace (EAF):
EAF technology utilizes electric energy to melt recycled scrap steel and produce new steel. By avoiding the use of coal or coke, EAFs have lower carbon emissions compared to traditional blast furnace-based steelmaking. Examples of EAF-based steel production include Nucor’s mini-mill facilities.
Carbon Capture and Storage (CCS):
CCS technology captures CO2 emissions from steel plants and stores them underground or utilizes them for other purposes. The captured CO2 can be stored in geological formations or used in enhanced oil recovery. CCS projects in steel manufacturing include the Acorn Project in the UK and the Port of Rotterdam CCS Project in the Netherlands.
“Net zero carbon technology in steel manufacturing faces various challenges, such as cost considerations, infrastructure development needs, feedstock availability and scalability, technological readiness and efficiency, regulatory and policy frameworks, and the importance of collaboration and knowledge sharing among stakeholders.”
Conclusion:
The significant carbon emissions associated with steel manufacturing pose a critical challenge that cannot be ignored. The current gap between emissions and carbon capture highlights the urgent need for effective decarbonization strategies in the industry. To mitigate the environmental impact and align with global climate goals, it is crucial to embrace decarbonization initiatives in steel manufacturing. Carbon capture and utilization (CCU) technology, with its ability to reduce emissions and generate value from waste, emerges as a vital component in our efforts to combat climate change and build a sustainable future. By implementing more environmentally responsible practices in coal utilization, the steel industry can make substantial progress towards decarbonization while still leveraging the advantages of coal as an energy source. Additionally, transitioning to net-zero carbon emission technologies without coal presents an opportunity for innovation and the creation of a more sustainable future for the steel industry and the planet. However, addressing the challenges related to cost, infrastructure, technology innovation, and policy frameworks is crucial for the successful implementation of these decarbonization strategies. By proactively addressing these challenges, the steel industry can lead the way towards a greener and more sustainable future.
Endnotes:
https://www.power-technology.com/news/tata-steel-hydrogen-injection-blast-furnace/
https://www.sciencedirect.com/science/article/pii/S0016236122033579
https://www.sciencedirect.com/science/article/pii/S0306261922000654
https://www.carbonclean.com/blog/steel-co2-emissions
https://www.netl.doe.gov/sites/default/files/netl-file/co2_eor_primer.pdf
https://worldsteel.org/wp-content/uploads/Biomass-in-steelmaking.pdf